Станкостроение: до и после реформы
Основу станкостроения составляет производство металлорежущих станков. Здесь в годы реформы произошел обвальный спад производства — более чем в 30 раз с 1990 г.:
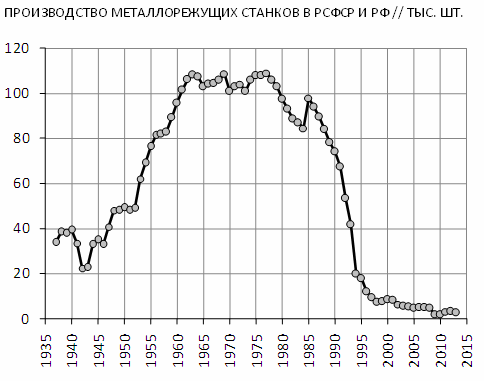
После 2000 г. стал быстро расти импорт металлорежущих станков. В 2000 г. он составил (за вычетом экспорта) 15,6 тыс. штук, в 2004 г. — 190 тыс., а в 2006 г. — 315 тыс. штук.
Это означает, что на рынке РФ станки отечественного производства практически полностью вытеснены импортными. Вызывает сомнение классификация станков в статистике импорта — один станок в среднем стоит около 1 тыс. долларов, что слишком дешево для обычного среднего станка. В 2012 г при производстве 3,4 тыс. металлорежущих станков, импортировано 673 тыс. станков за 1082 млн долл., а экспортировано 4,4 тыс. станков на 68,6 млн долл.
Особо надо сказать о производстве станков высокой и особо высокой точности, а также станков с числовым программным управлением (ЧПУ). Это — технологически наиболее передовая область станкостроения. В 1980-е годы она быстро развивалась, так что к концу десятилетия в РСФСР 23% выпускаемых металлорежущих станков были снабжены ЧПУ, а 11% относились к категории станков высокой и особо высокой точности. Это производство понесло самый большой ущерб:
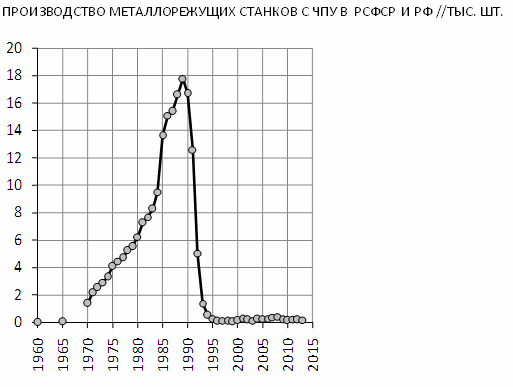
Если в 1990 г. в РСФСР было выпущено 16,7 тыс. станков с ЧПУ, то в 1996–1999 гг. их выпуск составлял по 100 штук в год — в 167 раз меньше.
В 2000 г. производство таких станков выросло в два раза и составило 200 станков. В 2001 г. было выпущено 257 станков с ЧПУ, а потом снова произошел спад, в 2010 г. — 129 токарных станков с ЧПУ и 31 обрабатывающий центр, агрегатный и многопозиционный (многооперационныйх) станок для обработки металлов, в 2011 г. — 195 и 8, в 2012 г. — 166 и 4.
Следует подчеркнуть, что речь идет не просто об уменьшении числа выпускаемых станков с ЧПУ, но и о том, что более наукоемкое производство оказалось подорванным в наибольшей степени.
При сокращении общего выпуска металлорежущих станков произошла не модернизация ассортимента, не снятие с производства устаревших типов, а, наоборот, технологический регресс — резко уменьшилась доля прогрессивной продукции в общем объеме производства. Аналогично доля станков высокой и особо высокой точности в общем объеме производства металлорежущих станков упала с 22,8% в 1989 г. до 1,3% в 1999 году. В 2012 г. доля производимых токарных станков с ЧПУ составляла 17%.
В результате реформы была разрушена важная наукоемкая отрасль машиностроения, предназначенная для разработки и производства автоматических и полуавтоматических линий для металлообработки и машиностроения. К 1985 г. отечественная промышленность вышла на уровень производства 754 комплекта линий, максимума их выпуск достиг в 1987 г. (802 комплекта), а с 1991 г. началось обвальное снижение выпуска, в 278 раз к 2009 г.:
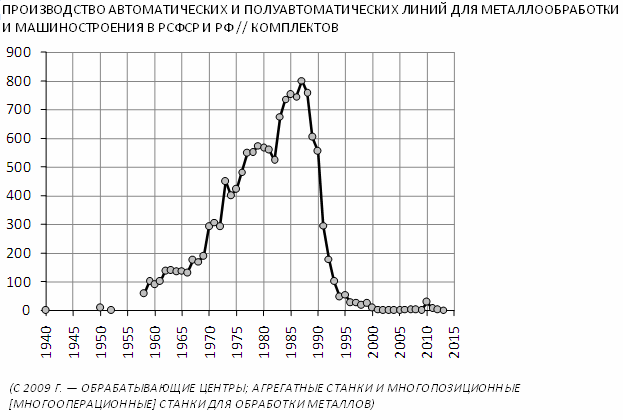
Важным направлением модернизации металлообработки в 1970-–1980-е годы была замена резания другими способами обработки — ковкой и прессованием. С этой целью быстро развивалось производство в РСФСР кузнечно-прессовых машин. С середины 80-х годов выпуск этих машин стал снижаться, а в годы реформы это направление было практически свернуто, и производство машин резко упало — почти в 40 раз. Заметного оживления его не наблюдается до настоящего времени:
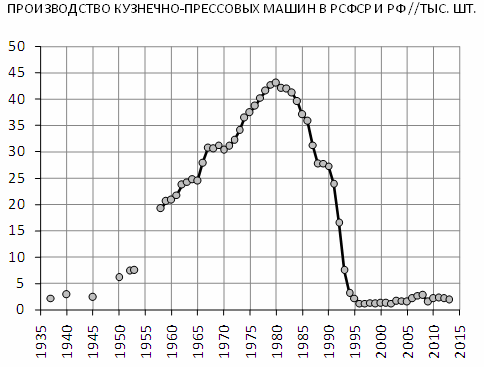
Надо подчеркнуть, что за время реформы был практически прекращен выпуск кузнечно-прессовых машин самого высокого технологического уровня — с числовым программным управлением. В 1990 г. было произведено 370 таких машин, а в 1997 г. — 3 шт., в 1998 — 4 шт., а в 1999 г. и 2001 г. — по 1 станку.
В 2005 г. производство несколько выросло — до 38 шт., в 2009 г. — 23 станка. В 2010 г было произведено 48 подобных станков с ЧПУ (машины гибочные, кромкогибочные, правильные, ножницы механические, машины пробивные и вырубные для обработки металлов), в 2011 г. — 39, в 2012 г. — 55, в 2013 г. — 50. В 2012 г. доля станков с ЧПУ в классе «Машины гибочные, кромкогибочные, правильные, ножницы механические, машины пробивные и вырубные для обработки металлов» составляла 3,1%.
Рассмотрим пару примеров из области машиностроения для легкой промышленности. Самое массовое производство в ней — текстильное. В нем две главные операции — прядение и ткачество.
В 1970-е годы в РСФСР производилось около 3,5 тыс. прядильных машин в год. Машин улучшенного типа выпускалось в 1980-е годы около 2,2 тыс. в год. С середины 1980-х годов ожидалась очередная модернизация этих машин. Однако начавшаяся реформа привела просто к свертыванию производства — выпуск прядильных машин упал к 1998 г. до 3 штук в год. В 2006 г. их выпуск составил 13 штук, в 2010 г. — 30, в 2013 г. — 10 станков. Спад производства в десятки раз означает, по сути дела, его ликвидацию.
Заметных изменений не происходит и в самые последние годы:
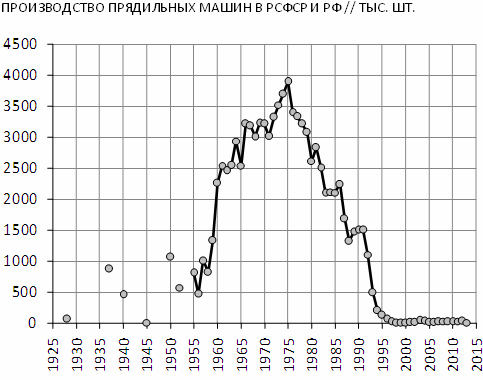
Машиностроительное производство, практически остановленное 20 лет назад, потребует для своего возрождения огромных средств. Но отказ от отечественного производства столь массовых машин и переход на их импорт обойдется еще дороже.
Судьба производства ткацких станков аналогична. Наивысшего уровня их выпуск достиг в середине 1970-х годов, в ходе модернизации текстильной промышленности. В 1980-е годы сохранялся почти стабильный уровень производства — 20–22 тыс. штук в год. Выпуск ткацких станков за годы реформы быстро упал в 200 раз, и восстановления этого производства не наблюдается. В 2010 г. выпущено 3 ткацких станка, в 2011 г. — 11, в 2012 г. — 64, в 2013 г. — 43 (в 1990 г. — 17,6 тыс.):
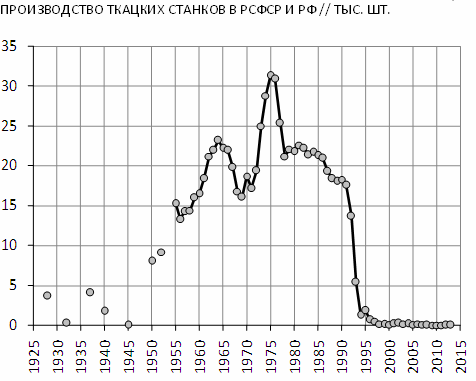
Резко сократилось в ходе реформы производство наукоемких изделий и приборов. Поскольку состояние этих производств во многом предопределяет безопасность страны, ссылки на то, что отечественные изделия не выдерживают конкуренции импортных образцов, несостоятельны, — поддерживать производственный потенциал таких отраслей приходится независимо от рентабельности. Так, в 2009 г. — по сравнению с 1990 г. — производство радиоприемных устройств сократилось в 55 раз.
Информация