Судостроительный завод «Залив» – как создать лидера судостроения на Черном море
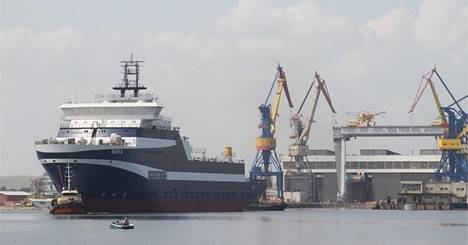
Изначально данная статья задумывалась как серия статей о судостроительном заводе «Залив». По ряду причин вынужден сократить объем текстов и уместить свои соображения в рамки сокращенной статьи. В частности, практически полностью были исключены разделы: история создания и производственные успехи завода во времена СССР, построенные суда и их судьба, факты перехода прав собственности и юридический аспект акционирования завода от момента развала СССР до предыдущего собственника в 2014 году.
Текущее положение завода по состоянию на конец 2021 года также пришлось дать в сжатом виде. Слишком много набралось материала и получилось малочитабельно для такой важной темы, как перспективы развития российского судостроения в Азово-Черноморском регионе на примере керченского завода. Возможно, в дальнейшем найду время для целого цикла статей по легендарному керченскому заводу, его прошлому, настоящему и будущему.
И еще. Статья готовилась до начала СВО на Украине и гибели флагмана Черноморского флота ракетного крейсера проекта 1164 «Москва». В свете этих событий актуальность предложений по реконструкции завода «Залив» переходит в острую необходимость скорейшего наращивания судостроительных мощностей. Как говорится, не судите строго, спел как мог!
Слава Богу – Крым наш! А вместе с ним и керченский судостроительный завод «Залив» имени Бориса Евстафьевича Бутомы. На данный момент это самое мощное судостроительное предприятие России в Азово-Черноморском регионе. Созданный в 1934 году «Залив» к 1980 году входил в число крупнейших судостроительных верфей Восточной Европы.
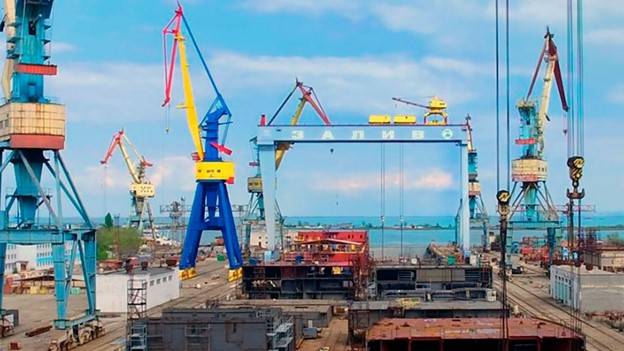
В сухом доке ССЗ «Залив» идет формирование корпусов судов
Вместе с судоверфями Херсона и Николаева завод успешно закрывал потребности СССР в гражданском и военном судостроении на юго-восточном направлении. Специализация керченского судостроительного завода «Залив» по состоянию на 1990 год – крупнотоннажное гражданское и среднетоннажное гражданское и военное судостроение. Завод также имеет опыт строительства судов с ядерной энергетической установкой – лихтеровоз «Севморпуть» проекта 10081, который с января 1988 года и по настоящее время успешно работает, обеспечивая Северный завоз на одноименных просторах.
Местоположение завода
Судостроительный завод «Залив» расположен в восточной части Крымского полуострова на берегу Керченского пролива, соединяющего Черное и Азовское моря. Он построен во внутренней акватории Камыш-Бурунской бухты и делит ее с портом «Камыш-Бурун».
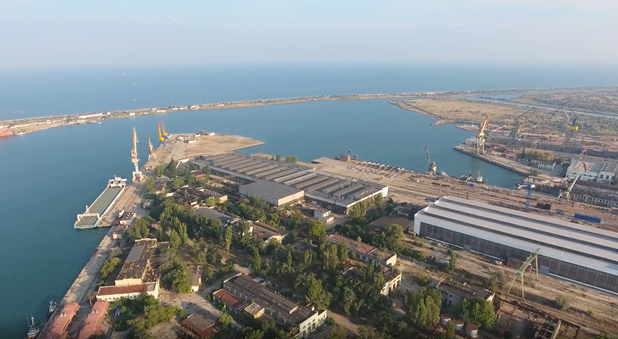
Вид на внутреннюю акваторию Камыш-Бурунской бухты и территорию судостроительного завода «Залив»
Завод имеет прямое морское сообщение с Азовским и Черным морями. Через Единую глубоководную транспортную систему Европейской части России (ЕГТС) – реки Волга и Дон с Балтийским и Каспийским морями. А также с судоходными реками Днепр, Южный Буг и Дунай, впадающими в Черное море, а через турецкие проливы со Средиземным морем. Доставка грузов для керченского завода возможна речным и морским, железнодорожным и автомобильным транспортом.
Расстояние до столицы Крыма г. Симферополя – менее 200 км, до главной военно-морского базы Черноморского флота России г. Севастополя – около 250 км, до главного порта Юга России и второй нашей ВМБ г. Новороссийска – 122 км. А «до ворот в центральную часть России» г. Азова – 327 км и г. Ростова-на-Дону на реке Дон – 357 км. Завод удачно расположен по отношению к морским и речным портам и военно-морским базам России в Азово-Черноморском регионе.
Расстояние от завода «Залив» до Крымского моста, автомобильное и железнодорожное сообщение которого соединяет Крымский полуостров с Большой Россией, около 8 км.
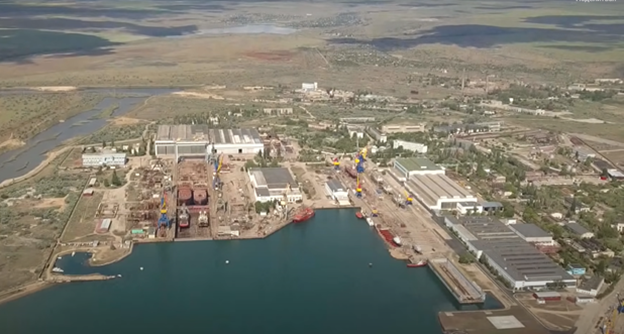
Общий вид на судостроительный завод «Залив» и Камыш-Бурунскую бухту
Природно-климатические условия для судостроения в Крыму намного лучше, чем, скажем, в Санкт-Петербурге, где Финский залив зимой на минимум 3–4 месяца может покрываться льдом. Незамерзающая Камыш-Бурунская бухта имеет глубины от 5 до 14 м и отгорожена Аршинцевской косой от Керченского пролива с глубинами до 18 м. Акватория бухты составляет около 2,5 км2 и зрительно разделена на судостроительную, достроечную и судоремонтную зоны. Примерно 1/3 бухты приходится на акваторию порта «Камыш-Бурун», который в настоящее время практически не функционирует.
Об истории завода
Государственный союзный Камыш-Бурунский судостроительный завод № 532 был основан в мае 1934 года. Свой первый заказ – пароход «Чапаев» водоизмещением 7300 т завод сдал 14 июня 1938 года, а в день начала Великой Отечественной войны 22 июня 1941 года был сдан первый военный заказ – торпедный катер типа Г-5.
Учитывая местоположение, завод изначально задумывался как один из крупных судостроительных заводов СССР. В советское время он развивался поэтапно, его строительство было прервано захватом Крыма фашистами и боевыми действиями против немецкий войск на Керченском полуострове. Восстановление разрушенного завода шло с 1944 до середины 50-х годов. Первой послевоенной производственной программой завода стала серия из девяти единиц сухогрузных барж проекта 411-бис грузоподъемностью 250 тонн каждая.
После глобальной реконструкции, завершенной в середине 1970-х годов, завод превратился в мощный универсальный судостроительный комплекс. Даже сейчас, в сравнении с крупнейшими питерскими верфями и строящейся новейшей суперверфью ССК «Звезда» в Большом Камне, судостроительный завод «Залив» выглядит очень достойно.
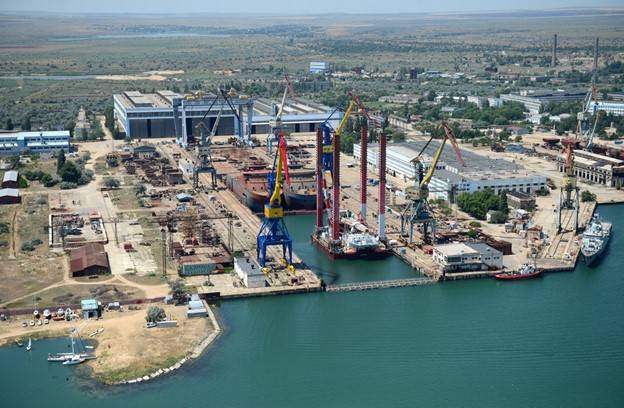
Вид на сухой док и основные производственные цеха судостроительного завода «Залив»
Описание завода
Из открытых источников мы имеем следующую информацию о заводе. Территория судостроительного завода «Залив» составляет 140 га. Суммарная площадь капитальных зданий более 212 000 м2, всего на территории завода 25 зданий площадью более 1 000 м2. Наиболее крупные цеха – корпусообрабатывающий, сборочно-сварочный и трубообрабатывающий, площадью от 24 000 до 75 000 м2, в которых расположены основные технологические участки завода. Большинство из них были сданы в эксплуатацию в 1960–1970-е годы.
Производственные мощности
Корпусообрабатывающее производство размещено в четырех пролетах блока корпусных цехов и включает:
• участок предварительной обработки металла со складом металла, оснащенный автоматической линией очистки и грунтовки металла и профиля фирмы «Гутманн». Линия была запущена в 1995 году и предусмотрена для дробеструйной обработки и грунтовки стали по стандартам ISO;
• автоматизированную линию по обработке прокатного листа и профиля с нанесением предварительного защитного слоя. Резка металла осуществляется в автоматизированном режиме машинами термической плазменной резки Suprarex SXE-P2 5500 (скорость резки до 24 м/мин или 0,4 м/с) и плазменными машинами «Кристалл» и «Гранат»;
• сортировочный участок и участок гибки деталей, оснащен прессами 5 000, 1 250 и 800 т.
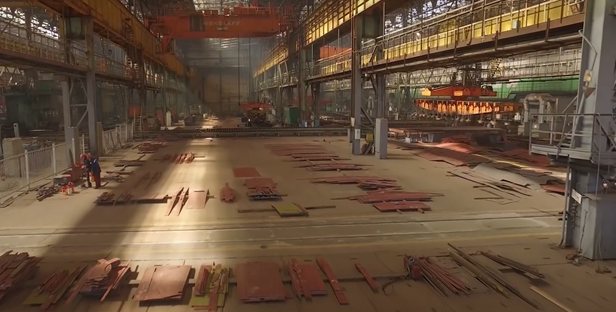
Цех корпусообрабатывающего производства – линия очистки и грунтовки металла
Производительность корпусообрабатывающего цеха керченского завода – 70 000 т стали в год. Для сравнения: это примерно равно мощности СЕВМАША (г. Северодвинск Архангельской обл.). А 1-я очередь дальневосточного ССК «Звезда» в Большом Камне составляет 90 000 т стали в год. После выхода обеих очередей на полную мощность «Звезда» будет обрабатывать 330 000 т судовой стали, что примерно равно суммарной обработке судовой стали всех остальных судоверфей, принадлежащих ОСК.
Сборочно-сварочное производство
• Производство расположено в пяти пролетах блока корпусных цехов. Общая площадь закрытых производственных помещений превышает 75 тыс. м2 и обеспечивает сборку блоков весом более 300 т и организацию работы в две смены.
• Сборочно-сварочное производство оборудовано крановым оборудованием грузоподъемностью до 200 т, а также линией сборки и сварки секций и блоков TTS (Норвегия). Линия обеспечивает производство панелей 12×18 м весом до 100 т, блоков корпуса 18×24 м весом до 300 т, 80 % секций и блоков изготавливаются на ней. Отдельно изготавливаются только носовые и кормовые секции.
• Цеха оборудованы кранами грузоподъемностью до 200 т и транспортными тележками грузоподъемностью до 350 т, площадь и высота закрытых производственных помещений достаточна, обеспечивает сборку блоков до 300 т и организацию работы в две смены.
Сборочно-сварочный цех завода имеет производительность 60 000 т металлоконструкций в год. В качестве поставщика для Крымского моста на «Заливе» было изготовлено суммарно около 2 000 т металлоконструкций.
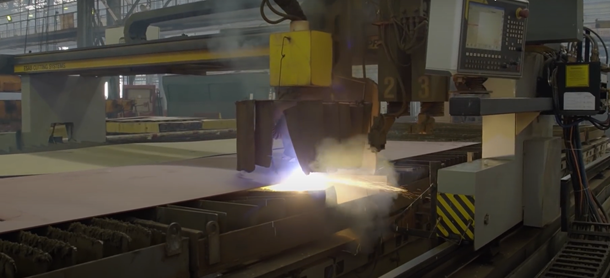
Цех корпусообрабатывающего производства – линия плазменной резки металла автоматизированной машиной
Трубообрабатывающее производство
• Имеет оборудование для выполнения всех основных операций по изготовлению судовых трубопроводных систем: трубогибочная машина ТГСВ-1/2, газорезательная машина БУГ-2 и трубогибочный комплекс Schwarze-Robitec для гибки труб от 42 до 220 мм, оборудование для промывки труб и гидравлических систем, проверки труб и арматуры гидравлики, а также участок гальваники, позволяющий производить горячее цинкование труб и других деталей погружением.
Мощность трубообрабатывающего производства составляет 70 тыс. м общей длины труб или 1 200 т/год.
Окрасочное производство
• Включает полный комплект технологического оборудования, обеспечивающего выполнение требований к защите от коррозии на всех стадиях постройки судна. Для выполнения окрасочных работ в 1994 году введен в эксплуатацию малярный цех, оснащенный технологическим оборудованием фирмы KISS (Германия).
• Малярный цех состоит из дробеструйного и окрасочного отделений. Ввод в эксплуатацию стационарного малярного цеха позволил увеличить объемы окрасочных работ на секциях и блоках до их монтажа в сухом доке или на стапеле с 25 до 75 %.
• Завод имеет оборудование для окраски внутренних поверхностей трубопроводов, освоенные и одобренные производителями красок технологии окраски грузовых танков для танкеров-продуктовозов и танкеров-химовозов.
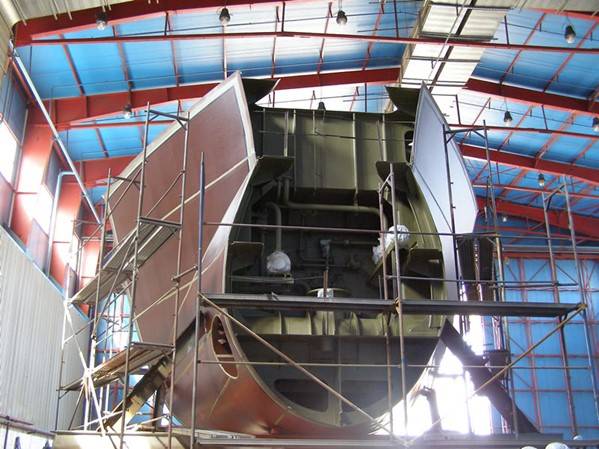
Окрасочная камера позволяет вести внутреннюю и внешнюю окраску блоков в комфортных условиях в любое время года
Общая производительная мощность цеха составляет 41 000 м2 окрашенных поверхностей стандартных судовых конструкций.
Механомонтажное производство
• Механомонтажное производство расположено на нескольких площадях. Имеется отдельный участок сборки главного двигателя, обеспечивающий сборку главной машины в объеме 100 % в цеховых условиях. Около 70 % всех механизмов устанавливается на борту в сборе, что существенно увеличивает скорость строительства.
Помимо этого, на территории завода расположен открытый склад металла и цех предварительной обработки металла. Отдельные технологические цеха, лаборатории и посты завода также включают:
• кислородно-ацетиленовую станцию;
• станцию сжатого воздуха, на 100 % обеспечивающую нужды завода;
• отдельные посты и лаборатории: неразрушающего контроля сварных швов, сварочную, механических испытаний, контрольно-измерительную;
• рентген-лабораторию (РЛ);
• химико-технологическую лабораторию (ХТЛ);
• санитарно-промышленную лабораторию (СПЛ);
• дозиметрическую лабораторию (ДЛ).
Специалисты завода обладают необходимым оборудованием и профессиональными навыками для выполнения всего комплекса судостроительных и достроечных работ, проведения швартовных и ходовых испытаний.
Судостроительные мощности
• Гордость завода – сухой док, имеет размеры 354×60×13,2 м. Можно использовать его как двухкамерный, обеспечивающий постройку (ремонт) судов на двух независимых позициях, длина каждой камеры дока может быть изменена путем перестановки съемного промежуточного затвора. Крановое оборудование сухого дока: козловые краны – 2 ед. грузоподъемностью по 320 т каждый, максимальная высота подъема кранов 60 м, позволяет формировать корпуса судов из блоков весом 400–600 т при их совместном использовании и портальные краны – 5 шт., грузоподъемностью по 80 т каждый.
• Потенциально существующий док позволяет строить суда длиной до 350 метров и шириной до 58 метров с водоизмещением до 300 000 т, а также до 2–3 судов одновременно. Если в советское время в сухом доке строились суда водоизмещением до 150 000 т, то сейчас сайт завода скромно заявляет о возможности строительства судов водоизмещением не более 70 000 т. Производственные мощности справятся, а вот состояние кранового оборудования и наличие необходимых квалифицированных кадров вызывает серьезные вопросы.
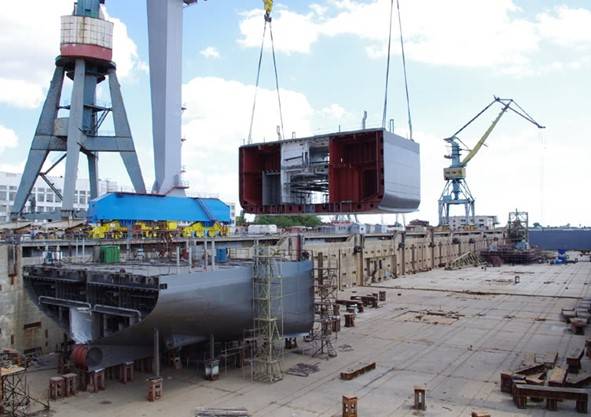
Сухой док – идет формирование корпуса судна из отдельных блоков. Суммарный вес готовых блоков с помощью двух козловых кранов типа «Галиаф» достигает 600 т
• Открытый стапель – две производственные линии по 400 м каждая, обеспечивающие постройку судов длиной до 130 м и шириной 22 м. Стапель оборудован 9 портальными кранами разной грузоподъемности: два крана по 80 т, три крана по 32 т и четыре крана по 16 т. Стапель имеет боковой спусковой слип Г-300 грузоподъемностью до 2 500 т. Для спуска судов водоизмещением 3 000–7 500 т используется плавдок «Кассандра» с ограничениями по габаритам.
• Производительность стапельного комплекса обеспечивает одновременное строительство 4–6 судов.
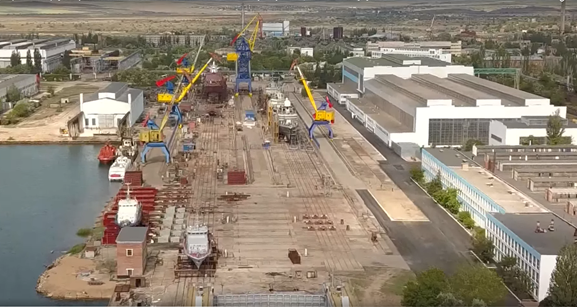
Вид на открытый стапель и спусковой слип – 27.05.2020 года. Справа (слева – верхнее фото) расположены крытый цех (дальний), где идет формирование и укрупнение блоков, и трубообрабатывающий цех (ближний)
• Общая протяженность достроечных набережных составляет 686 м. Достройка судов после спуска на воду производится на двух глубоководных причалах общей длиной 500 м, оснащенных портальными кранами грузоподъемностью: два по 32 т, один 50 т и один 80 т. Эти же причалы используются при выполнении судоремонтных работ. И набережной длиной 186 м с одним портальным краном грузоподъемностью 80 т, расположенной между открытым стапелем и сухим доком.
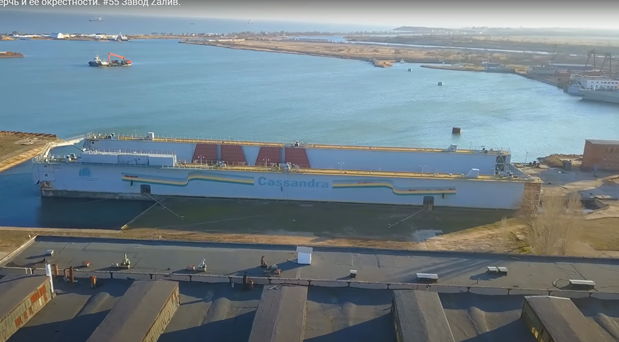
Передаточно-спусковой плавдок «Кассандра»
• Для проведения спусковых, швартовных и ходовых испытаний строящихся судов «Залив» располагает собственными производствами: плавдоком, плавучим краном грузоподъемностью 100 т, буксиром и водолазным катером. Территория завода оборудована ж/д путями, ведущими ко всем основным цехам и достроечным набережным.
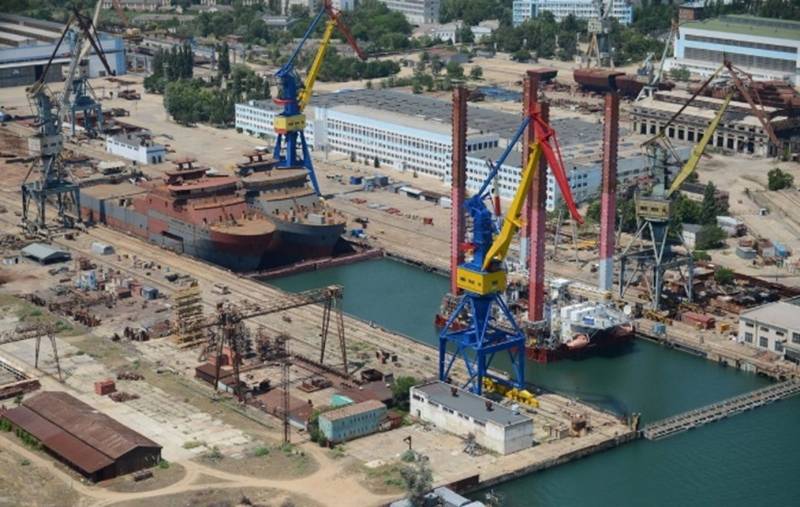
Сухой док используется для строительства судов и судоремонта. Большой вопрос в рациональности такого применения – мы теряем как минимум два стапельных места под строительство крупнотоннажных судов
В составе России – реализация программы модернизации и восстановления работоспособности завода
К моменту распада СССР «Залив» завершал строительство в сухом доке танкеров типа «Победа» проекта 12990 водоизмещением 65 000 т (серия из 16 танкеров строилась в 1980–1996 годах, причем 9 из них были построены на экспорт) и серии кораблей нескольких модификаций проекта 1135 для ВМФ и Пограничной службы на открытом стапеле. Один из которых «Гетман Сагайдачный» (заложен в 1990 году как «Киров») стал флагманом ВМФ Украины. Позже, уже во времена независимой Украины, была построена серия стационарных нефтяных платформ для Вьетнама.
Несмотря на потенциал, достаточный для ведения крупнотоннажного судостроения, завод в основном довольствовался заказами в сфере строительства офшорной техники и в качестве субподрядчика для заказчиков из Европы – 90 % продукции уходило на экспорт. С момента приватизации в 2000 году за 15 лет было построено 51 судно, суммарным водоизмещением менее 400 000 т, преимущественно судов снабжения, а также корпуса контейнеровозов, танкеров и сухогрузов водоизмещением от 2 000 до 35 000 т.
Назвать это успешной деятельностью сложно. Чтобы выжить, «Залив» открыл судоремонтное направление – на предприятии ежегодно ремонтировалось до 35 судов различного класса. Из-за спада объемов судостроительного производства резко усугубилось финансовое положение. После акционирования завод несколько раз переходил из рук в руки, меняя собственников. Произошла потеря квалифицированных кадров, с 2000 года было несколько волн сокращения штата сотрудников завода. Из-за отсутствия денег постепенно в нерабочее состояние стали приходить производственные корпуса и инженерные сети завода.
С присоединением Крыма в 2014 году судостроительный завод «Залив» начал оживать. Произошла смена руководства, на место менеджеров украинского собственника пришли представители коллектива завода и управленцы с Зеленодольского судостроительного завода. В настоящее время ССЗ «Залив» входит в состав АО «Судостроительная корпорация «Ак Барс» (СКАБ). Это позволило Зеленодольскому судостроительному заводу передать часть своих заказов на «Залив».
Завод получил финансирование на оперативный ремонт и новое строительство в размере 7 млрд рублей. С 2017 года началось активное поэтапное преображение завода. Разработана и выполняется программа реконструкции и нового строительства. За последние годы были введены в эксплуатацию после капитального ремонта блок корпусных цехов № 1 и построена новая кислородная станция мощностью 7 200 кг в сутки чистого кислорода. Отремонтированы цеха металлообрабатывающего производства, ведутся работы по ремонту и поддержанию технической готовности кранового хозяйства.
Начато технологическое перевооружение двух основных производственных цехов завода: корпусообрабатывающего и сборочно-сварочного. Для увеличения производительности корпусообрабатывающего производства будут приобретены и смонтированы – линия первичной обработки металла, линия резки профиля, две машины плазменной резки листового металла с ЧПУ, а также два мостовых крана с магнитными траверсами грузоподъемностью 25 т каждый.
Планируется проведение капитального ремонта магнитной системы позиционирования листов и замена морально устаревшего сварочного оборудования линии. Кроме того, для нужд этого производства приобретены два координатно-измерительных комплекса на базе лазерного тахеометра. Благодаря этому приобретению завод получил возможность проводить сверхточные угловые и линейные измерения изготавливаемых секций и блоков.
В рамках действующей программы по техническому перевооружению ведется пополнение парка автотранспорта завода. Недавно на завод для транспортировки негабаритных и тяжеловесных грузов был поставлен новый модульный транспортер грузоподъемностью 410 т. По своим характеристикам он значительно превосходит уже имеющийся грузоподъемный транспорт. Стоимость приобретенной техники составила 130 млн рублей.
В ходе подготовки производственных мощностей к исполнению новых перспективных заказов большое внимание уделено реконструкции инженерных коммуникаций: восстановлены энергосети открытого стапеля, достроечной набережной № 3 и БКЦ-1. Работы включали полную замену запорной арматуры и дефектных участков трубопроводов технических газов (кислород, ацетилен, сжатый воздух). Произведена замена 1,5 км силовых электрокабелей и 36 шкафов электроснабжения. Ремонтные работы затронули и крановое оборудование – окрашено по полной схеме 11 портальных и 12 мостовых кранов.
Действующая на заводе служба качества включает 4 испытательных лаборатории. Они выполняют контролирующие функции на всех стадиях технологического цикла – от входного контроля поступающих материалов, комплектующих и оборудования до подтверждения качества продукции после ее испытаний. Гарантией признания результатов измерений, выполняемых лабораториями, на уровне государственных и частных организаций является получение Центральной заводской лаборатории завода соответствующего аттестата аккредитации. В рамках подготовки к аккредитации на заводе проводится техническое перевооружение лаборатории.
Службой главного энергетика была проведена полномасштабная реконструкция системы водоснабжения докового комплекса. Для обеспечения сухого дока пресной водой, которая необходима для производственных нужд при проведении гидравлических испытаний судовых конструкций, а также для питания пожарного водовода. Кроме того, выполнена сложная технологическая операция по ремонту оборудования системы заполнения и опорожнения дока. Не менее значимой и ответственной задачей для инженерных служб стала работа по наращиванию высоты технических балконов, которые поднялись на 30 см, что теперь гарантирует коммуникациям защиту от затекания воды в тот период, когда идет заполнение дока. Общий объем финансирования по данному направлению составляет порядка 800 млн рублей.
В настоящее время «Залив» ведет набор специалистов по большинству судостроительных специальностей. Уровень заработных плат предлагается достойный, он вполне сравним с зарплатами на судоверфях Санкт-Петербурга и Дальнего Востока. В начале 2022 года произошла индексация всех действующих тарифных ставок и окладов в размере 6,3 % в целом по предприятию, а также увеличилась стоимость нормо-часа для основных производственных рабочих на 15 %. Это приблизило размер средней заработной платы основных рабочих производственных специальностей к 65 000 рублей. Понятно, что это средние зарплаты, но даже в объявлениях о приеме на работу предлагаются зарплаты от 30 000 до 80 000 рублей в месяц, а судовому слесарю-монтажнику в зависимости от уровня квалификации завод готов платить ежемесячно до 115 000 рублей.
Около года назад на судостроительном заводе началось внедрение специализированной промышленной информационной системы. В качестве платформы была выбрана российская информационная система Global-Marine, что в нынешних санкционных условиях имеет особое значение. Разработанная специально для предприятий судостроительной и судоремонтной отраслей России, она обеспечивает автоматизацию конструкторской и технологической подготовки производства, планирование и управление по всем его направлениям, включая финансовые и кадровые сектора.
Работа началась с внедрения блока автоматизации системы управления технологическим процессом. В настоящее время внедрение ПО на заводе уже затронуло несколько важных блоков, включая планирование производства, управление закупками и складом, а также конструкторский отдел и отдел главного технолога. Одновременно с этим закуплено и успешно опробовано печатно-полиграфическое оборудование для издательства завода. В течение ближайшего года на работу в АСУ будут переведены финансовый блок, отделы заключения договоров и управление складской логистикой, а также подразделения технического обслуживания и ремонта оборудования.
Все это позволит вывести завод на принципиально новый качественный уровень и сделать серьезный шаг к внедрению в дальнейшем безбумажного производства. Таким образом, деньги, выделенные на модернизацию завода, не проедаются, а точечно вкладываются в восстановление и развитие «Залива» на самых важных и ответственных участках.
Заказы для российского флота
За последние 8 лет завод получил заказы на строительство 22 кораблей и судов, большинство из которых пришли по линии ВМФ России. В июне 2017 года одновременно на заводе в работе находилось 17 заказов 7 различных проектов общим водоизмещением 64 000 т. И это помимо выполнения заказа на поставку 2 000 т металлоконструкций для Крымского моста. С 2014 года построены и спущены на воду два патрульных корабля проекта 22160 и три МРК проекта 22800, а также два кабельных судна проекта 15310. Заложены два средних морских танкера проекта 23131, два многофункциональных аварийно-спасательных судна проекта А163 и серия из 5 малых гидрографических судов проекта 19910.
Два крайних заказа являются знаковыми для «Залива» – 20 июля 2020 года были заложены два универсальных десантных корабля вертолетоносца проекта 23900 типа «Иван Рогов» водоизмещением 40 000 т. Появление этих заказов означает для завода переход на более высокий уровень сложности реализуемых проектов. Это вполне значимый, но далеко не полный список успехов завода за последние 8 лет.

Спуск на воду построенного на открытом стапеле судостроительного завода «Залив» МРК «Аскольд» проекта 22800 (республика Крым, г. Керчь, 21.09.2021 года)
Таким образом, с учетом всех проводимых изменений, на сегодняшний день судостроительный завод «Залив» полностью оснащен и работоспособен. Он обладает необходимым набором производственных цехов, оборудования и компетенций для выполнения заказов на строительство любых типов надводных военных кораблей и гражданских судов. Производственные мощности позволяют одновременно вести строительство 6–12 судов нескольких типов одновременно. Коллектив завода обладает должной квалификацией для выполнения заказов практически любого уровня сложности.
Завод готов строить широкую линейку гражданских судов: контейнеровозы, сухогрузы, лихтеровозы, балкеры и нефтерудовозы, танкер-продуктовозы и танкеры-химовозы водоизмещением до 150 000 т. Помимо этого, специалисты завода имеют опыт строительства военных кораблей 2–3 ранга и судов с ЯЭУ.
Вместе с тем длительные сроки строительства и нехватка стапельных мест являются наиболее проблемными местами для получения новых заказов.
Для примера – патрульные корабли 3 ранга проекта 22160 (2 ед.) и МРК проекта 22800 типа «Каракурт» (3 ед.) водоизмещением менее 2 000 т провели на открытом стапеле от 3 до 5 лет. Кабельные суда «Волга» и «Вятка» проекта 15310 водоизмещением 10 000 т каждый от закладки до спуска на воду провели в сухом доке, рассчитанном на крупнотоннажное судостроение, более 5 и 6 лет соответственно. Причины такой задержки вполне понятны – из-за принятых в отношении России и присоединения Крыма санкций оказалось невозможным получить из-за рубежа двигатели и многие комплектующие и завершить строительство. Но строить с такой низкой скоростью не самые сложные в изготовлении суда на крупном судостроительном предприятии и занимать надолго дефицитные стапельные места неприемлемо.
Практика мирового судостроения показывает, что каждые 30–50 лет судостроительные мощности требуют модернизации. Как мы знаем, с момента последней глобальной модернизации «Залива» прошло более 60 лет, и многие проектные решения, а также оборудование и механизмы, заложенные при модернизации в 60-е годы XX века, морально устарели.
За это время в мировом судостроении произошли серьезные изменения. Судостроительная отрасль прошла сквозь мощную волну цифровизации и автоматизации всех производственных процессов. Совершенствовались старые и появились новые технологии, сильно изменилось применяемое оборудование. Особенно радикально эти изменения сказались на развитии именно крупнотоннажного судостроения. То, что еще 30–40 лет назад считалось передовым и современным, на данный момент времени заметно устарело. Сравнительный анализ показывает, что оснащение лидеров мирового судостроения по сравнению с керченским судостроительным заводом «Залив» по многим направлениям ушло далеко вперед.
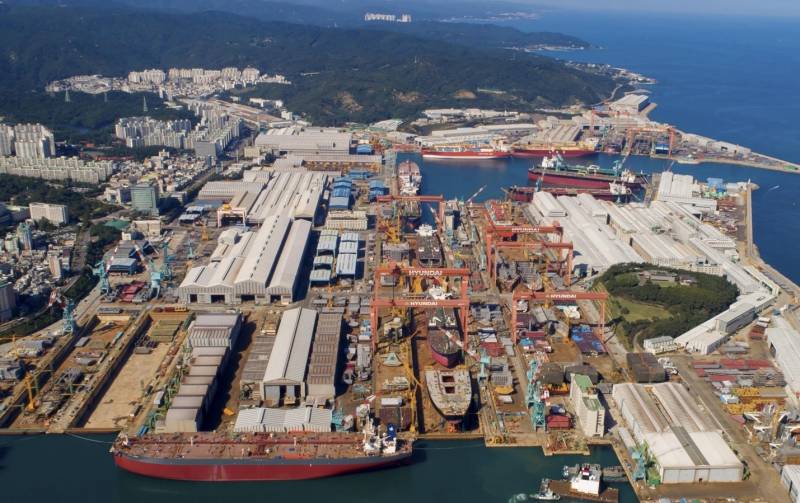
Пример сверхконцентрации судостроительных мощностей компании Hyundai Heavy Industries в г. Ульсан. На фото 5 сухих доков Hyundai’s Ulsan shipyard одной из 4 судоверфей и большое количество цехов по сборке блоков на одной производственной площадке. Всего только на этой верфи в г. Ульсан работают 9 доков длиной от 170 до 672 м. Корпорация Hyundai Heavy Industries обладает 3 судоверфями по крупнотоннажному судостроению и двумя отдельными подразделениями по офшорному и военному судостроению
Так, например, во многих странах-лидерах крупнотоннажного судостроения, произошла концентрация производственных судостроительных мощностей и ресурсов в одном месте. Наличие одного или нескольких сухих доков стало обычным даже для средних и мелких предприятий. Большое количество стапельных мест на крупных верфях позволяет вести строительство крупными сериями или нескольких судов разного типа одновременно с высокой производительностью.
При такой скорости строительства многократно увеличилось количество задействованных кранов разных типов, их грузоподъемность. Соответственно в разы увеличилось количество подъемно-спусковых операций и время работы кранов. Этому способствует слаженная работа одновременно нескольких цехов по сборке и укрупнению секций и блоков непосредственно на верфи и развитая кооперация с офшорными производственными площадками.
Грузоподъемность кранового оборудования для ведения крупнотоннажного строительства судов по сравнению с «Заливом» увеличилась в разы и еще 10 лет назад перешагнула за 2 000 т. В последнее десятилетие успешно освоено строительство судов готовыми блоками 3 000–5 000 т или полукорпусами до 10 000 т. Готовые блоки подразумевают установку трубопроводов, прокладку кабелей, монтаж оборудования и механизмов, а также установку судовых двигателей и отделку помещений.
На верфях произошло максимальное насыщение производственных цехов самым современным автоматическим оборудованием, полуавтоматическими инструментами и механизмами. Многократно сократилось использование объемов ручного труда, в десятки раз выросла скорость строительства и производительность труда судостроительных рабочих. Уже сейчас в Южной Корее на отдельных операциях используются роботы-сварщики и мини-роботы, помогающие прокладывать трубопроводы.
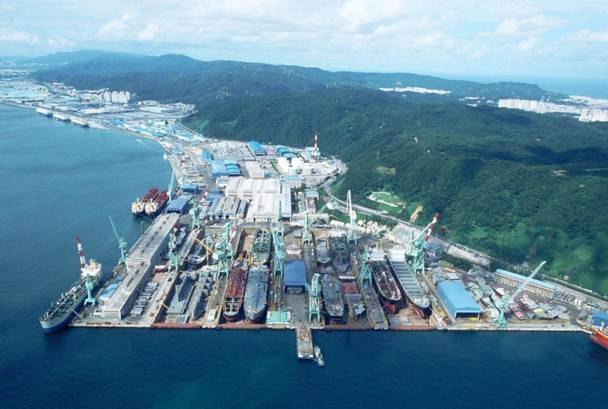
Судостроительные мощности промышленного конгломерата Hyundai Heavy Industries в г. Ульсан. В 4 сухих доках (3 дока 390×60 м и один док 300×70 м) компания Hyundai Mipo Dockyard Headquarters на одной производственной площадке ведется строительство крупнотоннажных до 12 судов одновременно. В Южной Корее располагаются 3 крупнейших мировых судостроительных компании Hyundai, Daewoo и Samsung, помимо этого, действует несколько десятков средних и мелких верфей
Чтобы шагать в ногу со временем керченскому «Заливу» требуется обновление по мировым стандартам. Учитывая, что других подобных производств на юге России у нас попросту нет, считаю необходимым сконцентрировать внимание государства и руководителей отрасли на развитии данного судостроительного завода.
В апреле 2021 года на заводе прошел технический совет по вопросам проектирования, подготовки производства к крупнотоннажному строительству. Участниками техсовета стали проектанты, инженерно-технические специалисты и корабелы. Обсуждались вопросы внедрения новых технологий и оборудования, а также их влияние на последующее снижение трудоемкости и затрат. Идет целенаправленная работа по возрождению завода и подготовке его к строительству крупнотоннажных судов.
Однако, надо признать, что в настоящее время заводу необходима масштабная реконструкция существующих и новое строительство судостроительных мощностей и полное переоснащение кранового хозяйства. На следующем этапе – расширение мощности производственных цехов, дальнейшее развитие производства и строительство новых судостроительных и судоремонтных мощностей.
На мой взгляд, уже сейчас необходимо думать о многократном расширении возможностей завода. Поэтому представляю на суд читателей свое видение – концепцию создания на основе судостроительного завода «Залив» крупнейшего центра судостроения Азово-Черноморского региона России.
Концепция развития судостроительного завода «Залив»
Судьба судоверфей Николаева и Херсона в условиях практически полной остановки всех судостроительных предприятий Украины на ближайшие годы остается неопределенной. Одни предприятия обанкротились и остановлены, другие находятся в частных руках их украинских владельцев. Если гражданское судостроение украинских верфей еще живо, небольшие заказы на судостроение и судоремонт выполняют регулярно, то с военным судостроением все печально, налицо практически полный развал производственных и судостроительных мощностей. Украинская судостроительная отрасль как единый производственный комплекс отсутствует.
Учитывая текущее состояние, надежды на быстрый запуск в работу украинских судостроительных предприятий немного. Но кто будет вкладывать деньги в развитие чужих предприятий? А смена собственников быстро вряд ли произойдет. По самым скромным подсчетам, на запуск еще живых предприятий при условии стабильного финансирования и одновременном запуске программы реконструкции в нормальный рабочий цикл потребуется 3–5 лет. Остальным потребуется не менее 5–10 лет для выхода на стабильный режим работы и крупные финансовые вложения в восстановление.
Острая нехватка судостроительных мощностей на Азово-Черноморском направлении и необходимость скорейшего строительства российского флота ставит вопрос срочного наращивания объемов производства на существующих российских верфях региона. С потерей флагмана Черноморского флота ракетного крейсера «Москва» стоит задача в максимально короткий срок увеличить численность кораблей 1–2 ранга. Даже для Азово-Черноморского региона наличие 5 вымпелов явно недостаточно, а с учетом необходимости постоянного присутствия наших морских сил в Средиземном море, требуется увеличение линейки кораблей типа эсминец или фрегат минимум в 3–4 раза. И это при одновременном наращивании объемов строительства гражданского флота, включая крупнотоннажное.
Опыт создания мощного судостроительного завода ССК «Звезда» на базе существующего судоремонтного предприятия в Большом Камне (Приморский край), где в настоящее время реализуется масштабный проект по строительству мощнейшей верфи, необходимо творчески переработать и применить при модернизации «Залива».
Расположение и территория керченского завода во многом напоминает планировку ССК «Звезда» – собственная территория с внутренним заливом и свободными земельными участками под реконструкцию и новое строительство. Важную роль играет наличие речного и морского, а также железнодорожного и автомобильного сообщения с европейской частью России. Расстояния от основных производственных центров страны в разы меньшие, чем на Дальнем Востоке.
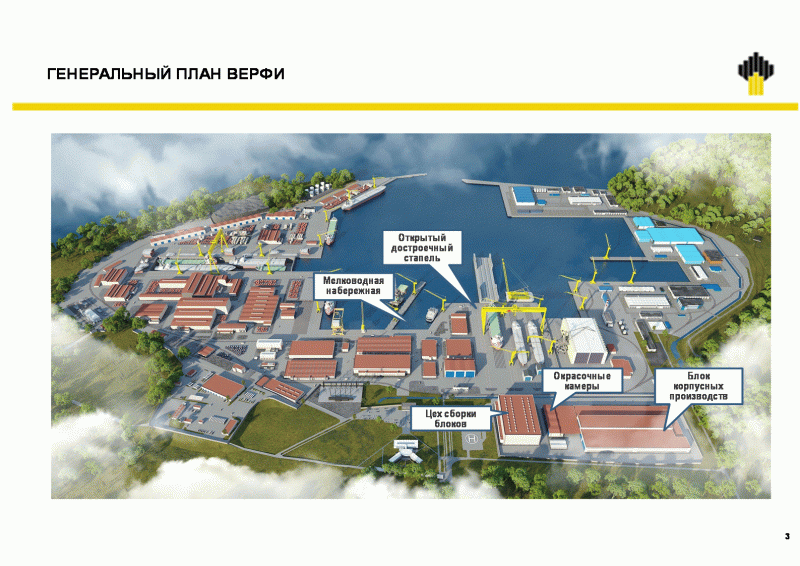
Генеральный план строительства I и II очереди судостроительного комплекса «Звезда», а также реконструкции и расширения судоремонтных мощностей ДВЗ «Звезда» г. Большой Камень, Приморский край (ССК «Звезда»: стапель – по центру, сухой док – справа, ДВЗ «Звезда» – справа и сверху). К сожалению, не нашлось места под строительство судоремонтных сухих доков для крупнотоннажных судов, строящихся на ССК «Звезда». Нет их и во всем Приморском крае, на Сахалине и Камчатке. Будем снова топить наши старые плавдоки или гонять суда в Южную Корею или Китай?
В обоих случаях рассматриваемые судостроительные заводы расположены в регионах, где присутствуют наши глубоководные гражданские морские порты и крупные военно-морские базы ВМФ России. При этом количество и качество отечественных судостроительных и судоремонтных мощностей в регионе в настоящее время явно недостаточно. Это подразумевает высокий спрос на гражданское и военное судостроение и на судоремонт. Что подтверждается объемами выполнения ремонтных работ наших гражданских судов в соседних странах и заказами на строительство на зарубежных верфях.
Данная концепция предусматривает на действующем судостроительном заводе в Керчи модернизацию существующего судостроительного производства, она включает:
1) модернизацию существующих судостроительных мощностей для повышения эффективности их использования (открытый стапель и сухой док);
2) расширение количества стапельных мест за счет реконструкции и нового строительства (открытый стапель);
3) строительство новых судостроительных мощностей (новый тяжелый стапель).
Для детального технологического аудита, анализа проектных и текущих возможностей завода требуется привлечение соответствующих профильных специалистов. Их отчеты и расчеты будут научно и инженерно-технически обоснованы. Даже предпроектная проработка высказанных мною предложений покажет степень их жизнеспособности.
В первом приближении озвучу наиболее серьезные проблемы завода:
Реконструкция существующих судостроительных мощностей
Открытый стапель
Оценочно, из открытых источников известно, что производственные линии открытого стапеля могут работать с корпусами (кораблей и судов) водоизмещением до 10 000 т с максимальными размерами – длина до 150 м и ширина до 21 м (это немного больше кораблей БПК проекта 1155/11551, но меньше ракетного крейсера проекта 1164 и вполне укладывается в размеры модернизированного фрегата проекта 22350М – оценочно 160×19 м). То есть открытый стапель позволяет строить корабли от ракетного катера до эсминца при спусковом весе до 10 000 т включительно. Все выше сказанное относится и гражданским судам.
Но существует проблема спуска на воду – имеющийся наклонный спусковой слип Г-300 обеспечивает спуск судов водоизмещением до 2 500 т, а спусковой плавдок «Кассандра», используемый на заводе, обеспечивает спуск на воду судов водоизмещением до 8 000 т с некоторыми ограничениями по габаритам. Основные проблемы открытого стапеля связаны с маломощным спусковым слипом и недостаточной загрузкой передаточно-спускового плавдока. Использовать спусковой слип для спуска судов водоизмещением более 3 000 т невозможно. Использование плавдока только для спуска на воду судов с открытого стапеля (сухому доку эта операция не требуется) делает подъемно-спусковые операции стапеля в целом низкорентабельными из-за большого времени простоя указанного оборудования в остальное время.
Еще одной проблемой является низкая скорость строительства судов, вследствие ограниченной грузоподъемности кранов, работающих на стапеле. Напомню, стапель оборудован 9 портальными кранами грузоподъемностью: два крана по 80 т, три крана по 32 т и четыре крана по 16 т. О состоянии кранов ярко говорит фото, представленное выше.
В итоге эффективность работы открытого стапеля остается низкой из-за больших постоянных расходов на содержание и ремонт одновременно маломощных кранов, спускового слипа и передаточно-спускового плавдока. Возможны два варианта решения данной проблемы.
Вариант № 1.
Отказ от имеющегося спускового плавдока, реконструкция спускового слипа и замена его на более грузоподъемный, замена кранов на более мощные (можно оборудовать стапель едиными кранами грузоподъемностью по 80 т снимаемыми после ремонта с сухого дока или новыми грузоподъемностью по 120 т). С противоположной стороны спускового слипа организуется продолжение открытого стапеля – строятся две новые производственные линии по 300 м каждая, оснащенные четырьмя кранами грузоподъемностью по 80–120 т.
Отечественные производители предлагают наклонные спусковые слипы с максимальным спусковым весом до 10 000 т. Аналогичные слипы были установлены в ходе реконструкции на ряде судостроительных заводов России. Замена спускового слипа на новый позволит отказаться от плавдока и на 100 % использовать потенциал, заложенный при проектировании открытого стапеля.
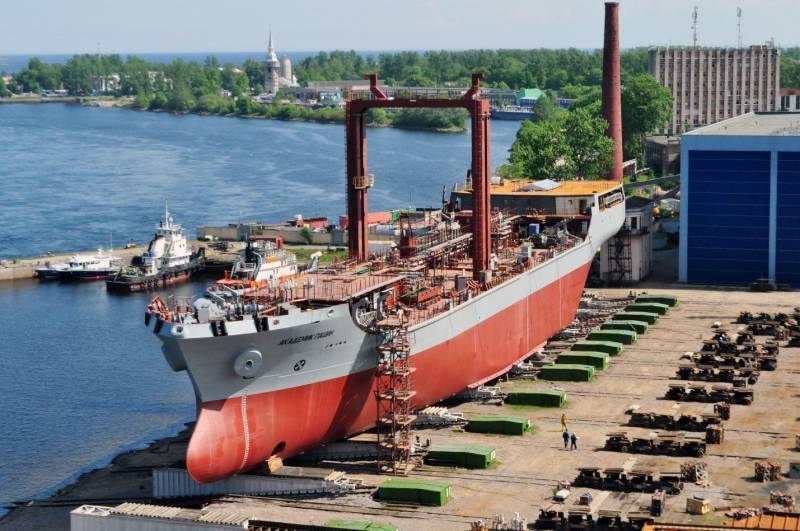
Танкер «Академик Пашин» проекта 23130 водоизмещением 9 000 т (размеры 130×21,5×7 м, максимальная скорость хода – 16 уз., максимальная дальность – 8 000 морских миль, автономность – 60 суток, экипаж – 24 человек, плюс 12 пассажиров) на спусковом слипе Невского судостроительного завода (г. Шлиссельбург, Ленинградская обл.). Два похожих танкера проекта 23131 заложены на «Заливе» еще в 2014 году
Место под размещение более мощного слипа и новой производственной линии есть, но потребуется восстановить часть набережной и намыть часть территории под новый участок стапеля. Ничего сложного в этом нет, подобные проектные решения применялись на других судостроительных и судоремонтных предприятиях еще во времена СССР. Некоторые судоверфи и судоремонтные заводы в СССР проектировались и имеют от 6 до 12 производственных линий при одном спусковой слипе. Также при строительстве новой линии стапеля потребуется перенос вертолетной площадки.
Этот вариант является наиболее экономичным. Он позволит с минимальными затратами увеличить в 1,5 раза возможности открытого стапеля и отказаться от использования плавдока, при этом количество операций спускового слипа вырастет в несколько раз.
Вариант № 2.
Полный отказ от спускового слипа и модернизация площадки для передачи строящегося судна сразу на плавдок, замена имеющегося спускового плавдока на более грузоподъемный. Так же как и в варианте № 1, с противоположной стороны от спускового слипа организуется продолжение открытого стапеля – строятся две новые производственные линии по 300 метров каждая, оснащенные 4–6 кранами грузоподъемностью по 80–120 т.
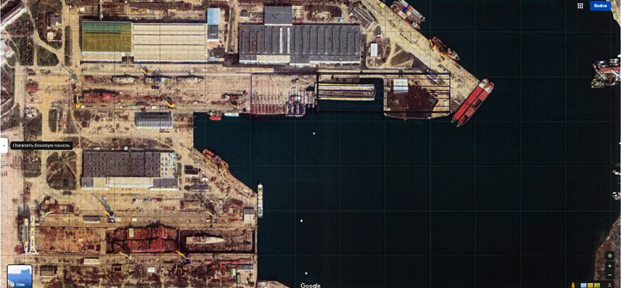
Место под размещение правого крыла открытого стапеля с 2 новыми производственными линиями и боковой передаточной площадки на плавдок
Этот вариант получается несколько дороже, но в итоге мы полностью демонтируем спусковой стапель, заменяя его на передаточную площадку.
В этом варианте предусматривается поперечная передача построенных судов сразу на новый плавдок типа «Вымпел» грузоподъемностью 40 000 т, аналогичный тому, который сейчас используется на ССК «Звезда». Он же будет задействован на спусковых операциях нового тяжелого открытого стапеля после его строительства (на старом стапеле – поперечная передача, на новом – продольная).
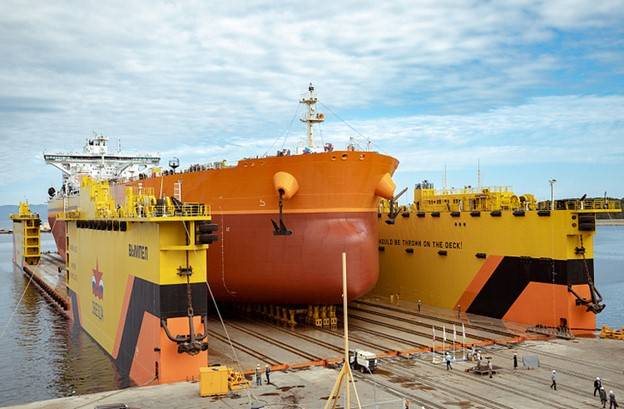
Передаточно-спусковой плавдок «Вымпел» на ССЗ «Звезда» в г. Большой Камень с первым построенным танкером «Владимир Мономах» (май 2020 года)
Отмечу также, что все работы по замене спускового слипа или по его замене на передаточную площадку с удлинением открытого стапеля и заменой кранов можно провести в сравнительно короткий период, поэтапно и практически без остановки судостроительных работ на самом стапеле. Что имеет немаловажное значение для устойчивой работы завода.
Теория подтверждается практикой и, возможно, я не прав, и оба варианта непроходные. Пусть соответствующие специалисты хотя бы предварительно оценят саму возможность использования такого решения, сделают и опубликуют предварительные расчеты. Будет интересно узнать полученные ими результаты.
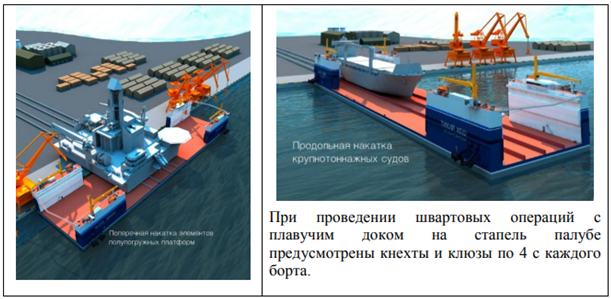
Продольные и поперечные передаточно-спусковые операции плавдока большой грузоподъемности – разработчик ОАО КБ «Вымпел»
В ходе реконструкции открытого стапеля имеет смысл привести к единому стандарту и повысить грузоподъемность портальных кранов. Для этого можно применить на старом участке открытого стапеля снятые с сухого дока и отремонтированные портальные краны грузоподъемностью 80 т или оснастить стапель новыми кранами грузоподъемностью 120 т. Снимаемые с открытого стапеля краны после капитального ремонта пойдут на обустройство расширяемых достроечных набережных.
Также имеет смысл просчитать возможность оснащения всего открытого стапеля еще более мощными козловыми кранами грузоподъемностью 320 т, снимаемыми с сухого дока. Даже за счет применения более мощных козловых кранов скорость строительства заказов и производительность труда открытого стапеля возрастет – прирост грузоподъемности составит 30 %.
Наличие четырех независимых производственных линий вдвое расширяет возможности открытого стапеля по одновременному массовому серийному строительству гражданских судов и военных кораблей разных типов: 4 производственные линии – 4 серии разных типов в работе. И это только на одном судостроительном участке завода.
Сухой док
Сам сухой док вполне современен, срок его службы определен по проекту не менее 100 лет. При должном обслуживании док прослужит еще долгие годы. Работы по его ремонту и модернизации уже ведутся или включены на ближайшее время в перспективный план завода. А вот крановое хозяйство сухого дока сильно устарело. Ремонтом механизмов и покраской кранов здесь не обойтись.
Грузоподъемность имеющихся козловых кранов по современным меркам не очень большая, и самое главное – она не соответствует проектным и потенциальным возможностям сухого дока. Потенциально размеры дока позволяют вести строительство судов водоизмещением до 300 000 т или нескольких крупнотоннажных судов меньшего водоизмещения и размеров одновременно.
Для эффективного строительства таких судов необходимыми условиями являются серийность и высокая скорость строительства. А повышение веса готовых блоков в 1,5–3 раза как раз и дает серьезный прирост скорости строительства. Поэтому сухому доку необходима полная замена козловых кранов на более мощные. Точное количество и их характеристики можно уточнить расчетом, предварительно видится замена двух козловых кранов грузоподъемностью по 320 т на новые 900–1 200 т.
Идеальным было бы приобретение козловых кранов в лизинг, их ускоренная амортизация и субсидирование процентных ставок по лизинговым платежам со стороны государства. Но, к сожалению, отечественная промышленность подобных кранов не выпускает, и данные условия на приобретенные за рубежом краны (в условиях санкций нам, скорее всего, будут доступны только китайские козловые краны, аналогичные тем, что установлены в Большом камне) не распространяются.
В рамках работ по модернизации не помешала бы и замена морально устаревших портальных кранов на новые отечественные грузоподъемностью до 120 т. Это даст прирост грузоподъемности портальных кранов на 30 %. После ремонта снятые с сухого дока краны можно использовать на других производственных участках. Например, при замене кранов на открытом стапеле, достроечных набережных или в ремонтных доках.
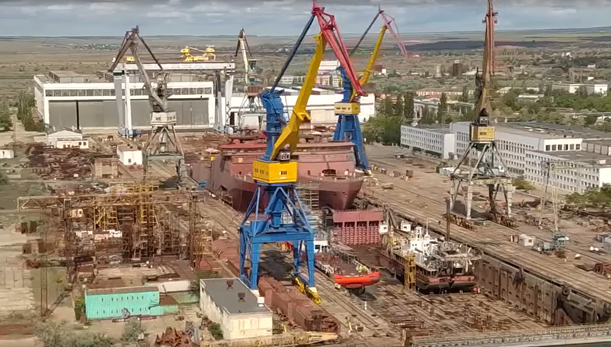
Вид на сухой док, в котором ведется строительство двух кабельных судов «Волга» и «Вятка» проекта 15310, и судоремонтные работы в отгороженной камере дока
Для повышения скорости строительства на преддоковой площадке сухого дока или рядом с ней целесообразно создать один или несколько крытых производственных участков (цехов) укрупнения блоков с 300–400 до 600–1 100 т. Это позволит вести параллельную сборку крупных блоков не только в производственных цехах, но и рядом с доком, формируя из нескольких более мелких один крупный блок.
Преимущества такого решения вполне очевидны – формирование больших блоков будет вестись одновременно сразу на нескольких площадках, сократится время простоя оборудования в производственных цехах и увеличится скорость строительства в сухом доке. Практика южнокорейских верфей показывает возможность собственной параллельной сборки на многих участках и офшорного строительства блоков на разных производственных площадках, и доставка готовых блоков к месту укрупнения или сразу к сухому доку для сборки морем. Почему бы не попробовать применить ее на «Заливе».
Новые судостроительные мощности
Открытый тяжелый стапель
Для выполнения нескольких больших заказов одновременно требуется в разы увеличить количество стапельных мест. Решение данной проблемы видится в строительстве нового тяжелого открытого стапеля. В качестве аналога предлагаю взять за основу тяжелый открытый стапель на ССК «Звезда».
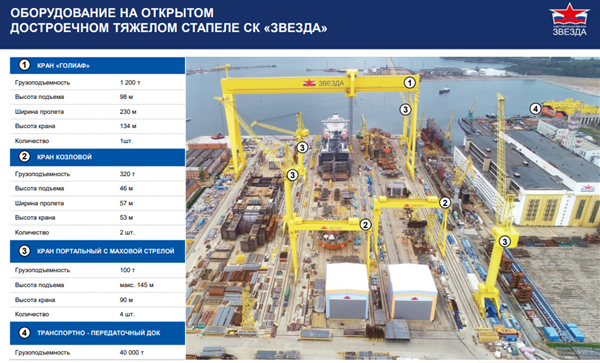
Открытый стапель на ССК «Звезда» – размеры 485×230 м с тремя производственными линиями, оборудован козловым краном типа «Голиаф» грузоподъемностью 1 200 т, двумя козловыми кранами – 320 т и четырьмя портальными кранами по 100 т каждый (г. Большой Камень, Приморский край)
Территория завода «Залив» позволяет разместить новый тяжелый стапель параллельно существующему сухому доку. Оценочно, на рассматриваемой территории возможно построить тяжелый стапель с двумя производственными линиями, протяженностью до 600 м и шириной до 60 м каждая. Для нового стапеля потребуется намыть небольшой кусок территории и углубить дно перед ним до проектных величин, необходимых для спуска судов на воду.
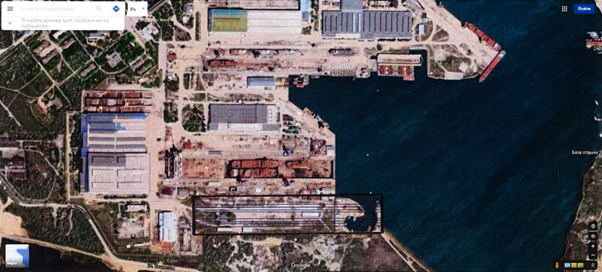
Место под размещение нового открытого тяжелого стапеля
Расстояние от действующих производственных цехов до нового стапеля увеличится незначительно, поэтому доставка готовых блоков будет осуществляться с помощью самоходных транспортных систем так же, как и на преддоковую площадку сухого дока.
Стапель требуется оснастить мощным крановым оборудованием:
• козловой кран типа «Голиаф» грузоподъемностью 1 200 т – 1 ед.;
• козловые краны типа «Голиаф» грузоподъемностью 320–600 т – 2 ед.;
• портальные краны грузоподъемностью 120 т – 4–6 ед. (уточнить расчетом).
Появление нового тяжелого стапеля позволит максимально загрузить производственные мощности завода и одновременно расширит количество закладываемых, строящихся и спускаемых на воду типов судов.
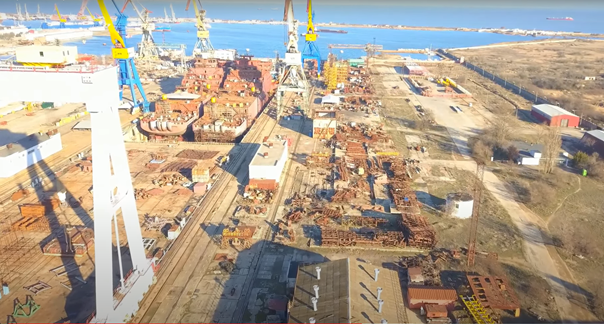
Территория под размещение нового открытого тяжелого стапеля – справа от кранов сухого дока
Для спуска судов на воду тяжелому стапелю потребуется транспортно-пусковой плавдок большой грузоподъемности, аналогичный тому, что имеется в распоряжении ССК «Звезда» в Большом Камне (Приморский край). Однако используемый на «Заливе» будет немного отличаться, при его заказе необходимо учесть возможность продольного и поперечного выполнения передаточно-спусковых операций. Этот же плавдок будет использоваться для спуска на воду судов модернизированного существующего открытого стапеля, о чем уже указано выше (см. раздел Существующий открытый стапель – вариант № 2). Имеет смысл оценить возможность его использования в качестве судоремонтного плавдока.
Создание нового тяжелого стапеля на «Заливе» обеспечит прирост количества стапельных мест примерно в 2,5–3 раза. Большая протяженность каждой производственной линии нового стапеля даст возможность закладывать и вести строительство на каждой из них двух-трех судов разных типов одновременно.
Альтернативным вариантом может стать создание на этом же месте второго сухого дока размерами 500×100×14 м. Однако такое решение представляется менее эффективным из-за больших затрат на строительство и меньшего количества новых построечных мест. К тому же, по оценкам специалистов Центра технологий судостроения и судоремонта (ЦТСС), строительство сухого дока обойдется ориентировочно на 10–15 % дороже возведения открытого стапеля.
В случае исчерпания возможностей наращивания объемов имеющихся производственных цехов, имеет смысл еще при проектировании нового тяжелого стапеля предусмотреть возможность расширения действующих цехов или организации приема готовых блоков с офшорных производств с воды. Такое решение позволит организовать кооперацию и загрузить предприятия, расположенные на Дону и Волге. Заказы на изготовление отдельных секций или готовых блоков можно размещать как на судостроительных, так и судоремонтных верфях. Тем самым решается застарелая российская проблема – низкой загрузки этих предприятий.
В качестве идеи – имеет смысл просчитать возможность заказа на резку судовой стали, изготовление наиболее простых секций или отдельных блоков весом до 150 т на производственных мощностях крупных металлозаводов, расположенных вдоль крупных рек европейской части России. Применяемые этими металлозаводами в производстве металлоконструкций и изделий из металла технологии сварки и оборудование во многом схожи с технологиями судостроения. Необходимо использовать такой потенциал.
Судостроительному заводу достаточно ограниченного количества постоянных поставщиков для кратного увеличения объемов производства готовых блоков. А доставку на «Залив» можно организовать по единой глубоководной транспортной системе (ЕГТС) речным транспортом.
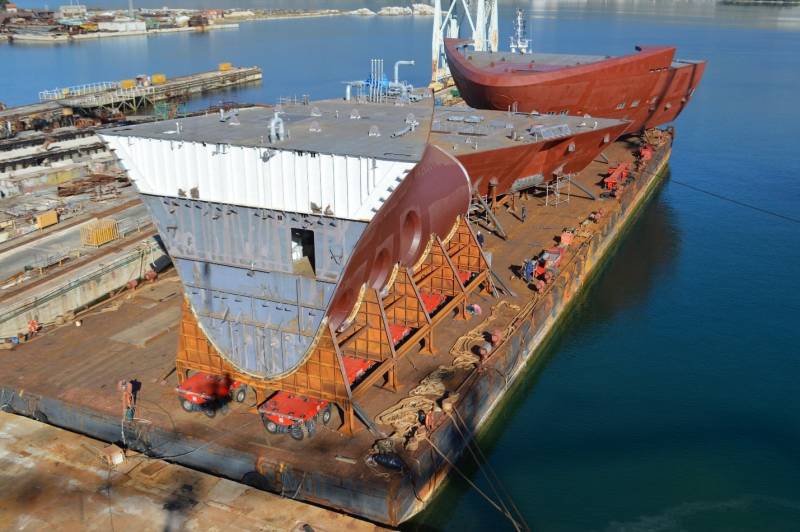
Доставка готовых блоков на несамоходной барже с офшорной производственной площадки к месту сборки судна (Южная Корея, 2010 г.)
Выводы
Модернизация существующих мощностей и новое строительство на заводе «Залив» кратно расширят количество стапельных мест, позволят максимально загрузить имеющиеся производственные цеха, снизят время простоя оборудования и увеличат скорость строительства. Это повысит эффективность использования судостроительных мощностей и даст возможность гибко подходить к формированию производственных планов завода. В разы увеличит число закладываемых и спускаемых на воду судов.
В итоге после реализации всех предложенных мер мы получим в Азово-Черноморском регионе универсальный судостроительный завод, оснащенный современным оборудованием и соответствующий всем требованиям, предъявляемым к крупнейшим судостроительным верфям мира. Его специализацией будет средне- и крупнотоннажное гражданское и военное судостроение. Было бы неплохо также нарастить и судоремонтные мощности завода путем строительства судостроительно-судоремонтных сухих доков, но это более отдаленная перспектива, требующая отдельного расчета и пояснений, выходящих за рамки представленной концепции.
Главное – керченский судостроительный завод «Залив» после завершения модернизации своих мощностей позволит закрыть значительную часть потребностей России в Азово-Черноморском регионе в строительстве гражданских судов и военных кораблей практически любого типа и водоизмещения. Основными вопросами успешной реализации всего предложенного будет стабильное финансирование и наращивание объемов госзаказа по строительству гражданского и военного флота. Российского флота, которого так не хватает сегодня!
Информация