Технологии победы: автоматическая сварка танковых корпусов
Укрощение брони
Одной из основных проблем производства корпусов и башен средних танков Т-34 было трещинообразование в местах сваривания деталей. Все дело в высокой твердости брони 8С, когда рядом со сварным швом образовываются небольшие надрывы или микротрещины. Наличие остаточных напряжений после сваривания в первое время после производства бронемашины не давало о себе знать, но с течением времени выходило наружу трещинами длиной до 500 мм. Все это, естественно, снижало ударную стойкость танковой брони. Для решения этой проблемы сразу после организации производства эвакуированных предприятий, во второй половине 1942 года, привлекли специалистов Броневого института (ЦНИИ-48) и Института электросварки Академии наук СССР. Исследования проводились на двух предприятиях: Уральском танковом заводе №183 в Нижнем Тагиле и Уральском заводе тяжелого машиностроения в Свердловске. В общей сложности с июля по октябрь металлурги и материаловеды исследовали образование трещин при сваривании около 9500 бронедеталей. Целью изучения был поиск наиболее оптимального химического состава брони 8С. Оказалось, что наиболее важным компонентом в броне в этой ситуации был углерод. В случае, если его содержание в броне было больше 0,25%, твердость закаленной зоны в районе сварного шва резко возрастала, что неминуемо приводило к трещинообразованию.
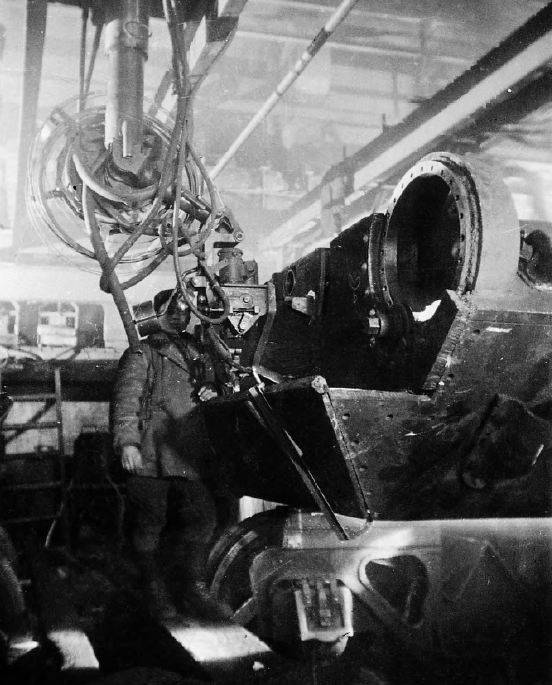
Но обеспечить такое низкое содержание углерода в броневой стали и в мирное время было непросто, а в условиях военного времени вообще казалось невозможным. Небольшие «косметические» изменения сварочного цикла путем использования аустенитных электродов, многоваликовой системы наложения сварных швов и низкий отпуск узлов после сварки позволяли поднять верхний предел содержания углерода лишь до 0,28%. Кстати, в немецкой танковой промышленности о столь серьезных требованиях к танковой броне и не слышали – в среднем доля углерода была в пределах 0,4-0,5%. Решением проблемы появления трещин в области сваривания оказался предварительный нагрев деталей до 150-200 градусов Цельсия с последующими медленным остыванием деталей после сваривания до 100 градусов в течение 30 минут. Для этой цели в Броневом институте были разработаны специальные индукторы, обеспечивающие локальный нагрев бронедеталей в зоне газовой резки либо сварочного шва. На Уральском заводе тяжелого машиностроения индукторы применялись при сваривании стыка лобовой части с бортами и крышей, а также при вырезании балансирных отверстий в закаленных бортовых деталях танков. Таким образом была решена проблема трещинообразования при сваривании среднеуглеродистых бронесталей. Со временем практика свердловского завода была распространена на остальные танковые заводы.
Сварочные автоматы
В июле 1941 года распоряжением Совета Народных Комиссаров в Нижний Тагил был эвакуирован Институт электросварки Академии наук СССР. Именно поэтому на Уралвагонзаводе впервые была внедрена автоматическая дуговая сварка танковых корпусов под флюсом. Безусловно, эта технология был известна и ранее, но группа академика Евгения Оскаровича Патона с сотрудниками ЦНИИ-48 смогли адаптировать её для сварки броневых сталей. Одним из выдающих ученых, внесших вклад в развитие бронетанкового сварочного дела, был Владимир Иванович Дятлов. Он вместе с сотрудниками Харьковского завода имени Коминтерна решил проблему трещинообразования в броне при сварке путем введения в сварочную ванну низкоуглеродистой проволоки (подробнее об этом пойдет речь ниже). В 1942 году ученый, первый в мире, открыл явление саморегулирования дуговых процессов с плавящимся электродом, что позволило значительно упростить конструкции подающих механизмов сварочных автоматов. Также за счет этого удалось создать относительно простые одномоторные сварочные головки, более надежные и дешевые. Без Дятлова не удалось бы создать эффективные флюсы на основе шлаков доменных древесно-угольных печей Ашинского металлургического завода, которые получили названия «шлаковые флюсы ША». С октября 1943 года ученый возглавил лабораторию сварочного Уралвагонзавода и пробыл на этой должности до 1944 года, пока его не перевели в ЦНИИ Технологий судостроения.
Но вернемся к легендарному Т-34, который никогда бы не стал таким массовым танком, если бы не автоматическая сварка его бронекорпусов (башен) на заводах №183 и УЗТМ. Использование сварочных автоматов позволяло сократить время на сварку в 3—6,5 раза. При этом на каждый танковый корпус использовалось не менее 40 погонных метров сварочных швов.
Кроме Т-34, сварка академика Патона применялась на бронекорпусном заводе №200 в Челябинске. С её помощью варили днище корпуса танка КВ, что в общей сложности составляло около 15 погонных метров шва на одну машину. Немаловажно, что автоматизация сварки брони позволила привлекать к производству низкоквалифицированных рабочих – мастеров-сварщиков на протяжении всей войны хронически не хватало. В Нижнем Тагиле с июля 1942 года работал уникальный танковый конвейер, на котором действовало 19 установок автоматической сварки под флюсом. Оцените масштаб новации — это позволило высвободить для других работ 280 высококлассных сварщиков, заменив их 57 рабочими низкой квалификации. Сам академик Евгений Оскарович Патон в докладной записке на имя секретаря отдела танковой промышленности Свердловского обкома ВКП(б) в марте 1942 года говорил об эффективности внедрения автоматической сварки (цитата по книге Н. Мельникова «Танковая промышленность СССР в годы Великой Отечественной войны»):
Сравнение затрат времени на ручную и автоматизированную сварку можно найти в архивах выставочного комплекса ОАО «НПК Уралвагонзавод». В соответствии с ними, на сварку, к примеру, сектора погона башни Т-34 у сварщика уходит чуть более пяти часов, а автоматическая сварка справляется с этим всего за 40 минут. Стыки днища с помощью ручной сварки провариваются за три часа, а в автоматическом режиме — за один час.
Борьба за шов
Нельзя сказать, что автоматические сварочные аппараты в одночасье появились на сборочных предприятиях советского танкопрома. Во-первых, доля ручной сварки все-таки была очень велика в производстве бронепродукции, а во-вторых, на первых порах с самой технологией не все было гладко. Не удавалось придать сварному шву необходимый уровень пластичности – после остывания он становился твердым и хрупким. Это, естественно, самым негативным образом сказывалось на снарядостойкости брони. После разбора причин оказалось, что все дело в превышении глубины проплавления свариваемого металла, перемешивании металла проволоки с основным металлом и значительном легированием металла шва. Группы из ЦНИИ-48 под руководством И. Ф. Срибного и из Института сварки, во главе которой стоял упоминаемый выше В. И. Дятлов, предложили и апробировали следующие приемы сварки «непокорной» брони 8С и 2П. Прежде всего это многопроходная сварка, когда автомат за несколько приемов соединяет свариваемые детали. Так обеспечивается малое проплавление стыков и формированием прочного и пластичного шва. Понятно, что такой прием не самый эффективный в условиях военного времени: все-таки многопроходная сварка требует большое времени в сравнении с однопроходной.
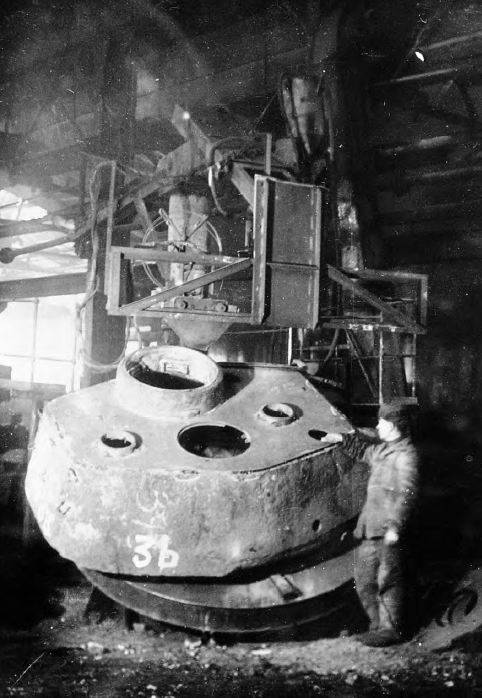
Вторым приемом от ЦНИИ-48 и Института сварки была закладка проволоки из малоуглеродистой стали в разделку швов для снижения «разваривания» металла брони. В итоге шов после остывания становился пластичнее, проволока серьезно снижала температуру внутри разделки шва, а также в два раза увеличивала производительность сварочных автоматов. Это оказалось наиболее эффективным приемом, который в дальнейшем был даже усовершенствован. Новый способ сварки «в две проволоки», при котором в ванну шва под углом к электродной проволоке подавалась вторая (присадочная) проволока, не подключенная к источнику тока. Подачу и диаметр второй проволоки рассчитывали таким образом, чтобы количество наплавляемого от нее металла было равно количеству металла от наплавляемой электродной проволоки, то есть диаметр второй проволоки должен быть равен диаметру электродной проволоки и скорости их подачи должны быть одинаковыми. Однако в связи с необходимостью переоборудования автоматических головок с подачи одной проволоки на подачу двух внедрение этого способа было отложено и он был заменен способом с закладкой прутков. Тем не менее, уже в июне–июле 1942 года этот способ был применен на заводе № 183 при сварке партии нижних листов носа корпуса танка с носовыми балками.
Сложности с автоматизацией сварки танковых корпусов (башен) были и организационного плана. Стоит помнить, что никогда ранее сварочные автоматы не собирались серийно и были, по сути, продуктами опытного производства Института сварки. Это и объясняет некоторую медлительность в освоении новых технологий в танкопроме. Так, к концу 1942 года на танковых заводах было всего от 30 до 35 сварочных автоматов, которых, естественно, не хватало. Поэтому нарком И. М. Зальцман приказом №200с от 28 марта 1943 года распорядился на заводе №183 дополнительно установить до середины мая 7 автосварочных агрегатов, на Уральском заводе тяжелого машиностроения до 1 июня 8 автоматов и до 15 июня 5 агрегатов требовал поставить на челябинский завод №200. Этот шаг стал один из многих, позволивших отечественному танкопрому выйти на плановые показатели производства столь необходимой фронту гусеничной бронетехники.
Продолжение следует…
Информация